Unlocking Efficiency with IC Decapsulation in Printed Circuit Boards
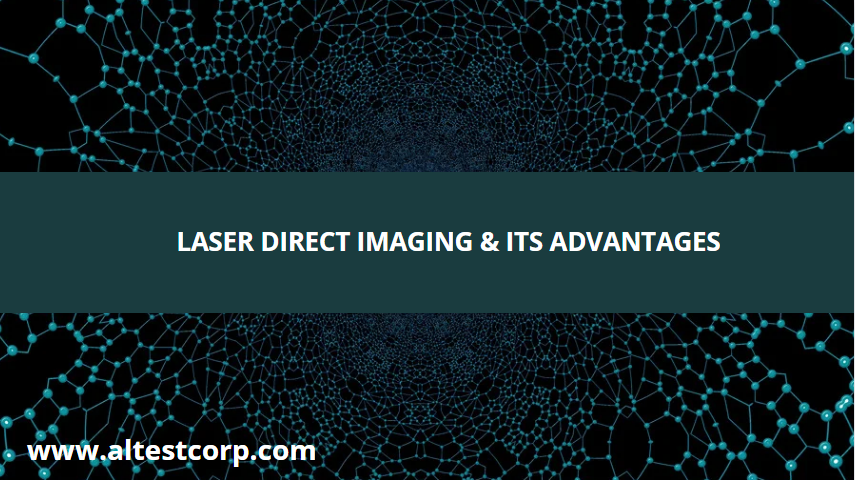
Admin, March 28,2024
Laser Direct Imaging in Printed Circuit Boards
Optimizing Flexibility and Durability
Laser direct imaging (LDI) is a technology used to create images on PCBs. This technology is used in various industries, including the electronics, automotive, and medical industries. LDI is a very versatile technology that can create multiple images, including logos, text, and patterns.
There are many benefits to using LDI in PCBs. One of the main benefits is that LDI is an exact technology. This suggests that it can be used to create very intricate images on PCBs. Additionally, LDI is a high-speed technology. This means that images can be created quickly and easily.
Overall, laser direct imaging (LDI) is a very versatile and precise technology that can create various images on PCBs. While there are some drawbacks to using this technology, the benefits far outweigh the drawbacks.
What is Laser direct imaging (LDI)?
Laser direct imaging (LDI) is a process of printing in which a laser beam is used to remove material from a substrate selectively. This process can create patterns or images on various materials, including plastics, metals, and glass. LDIs are often used in producing semiconductor devices, printed circuit boards, and other electronic components.
LDI has several advantages over traditional photolithographic techniques. It is much faster, allowing for higher throughput in the manufacturing process. It is also more flexible, allowing for the imaging of complex shapes and patterns. Additionally, LDI is more precise, resulting in higher yields and fewer defects.
Despite these advantages, LDI has several drawbacks. It is more expensive than traditional photolithographic techniques, and the laser used in the process can damage the resist if not properly controlled. Additionally, the process is somewhat complex and requires skilled operators to produce high-quality results.
What are the uses of Laser direct imaging (LDI)?
Laser direct imaging is a powerful tool for creating high-quality prints. It suggests several advantages over traditional printing methods, including superior print quality, greater accuracy, and increased speed.
Laser direct imaging can produce prints with excellent details and accurate colors. This makes it ideal for printing photographs and other images that require high levels of detail and accuracy. In addition, direct laser imaging is much faster than traditional printing methods, making it ideal for high-volume printing applications.
Why is Laser Direct Imaging used in Printed Circuit Boards
LDI is a process that uses a laser to direct-write images onto a substrate. It is commonly used in manufacturing printed circuit boards (PCBs). LDI offers several benefits over traditional methods of PCB manufacturing, such as photolithography.
LDI is a much faster process than photolithography and can be used to create very complex designs. It is also a more versatile process, capable of producing a wide range of features on a substrate.
It is a relatively new technology, and as such, it is constantly evolving. This means that it is continually becoming more capable and more cost-effective. This is why LDI is becoming increasingly popular for use in PCB manufacturing.
Laser Direct Imaging (LDI) is a technology for imaging patterns onto printed circuit boards (PCBs). LDI uses a laser to direct light onto the PCB, which is then exposed to light-sensitive film. The film is then developed, and the resulting image is used to create the PCB.
It is an exact and accurate way to create PCBs and is becoming increasingly popular as technology improves. It offers several advantages over traditional methods, such as photolithography, including higher resolution, shorter exposure times, and the ability to create minimal features.
It can create features as small as 10 microns and is ideal for creating high-density PCBs. It is also very universal and can be used to create a variety of different patterns.
Overall, LDI is a highly effective way to create PCBs and is likely to become even more popular as technology develops.
History:
The history of direct laser imaging in printed circuit boards (PCBs) goes back to the early 1990s when the first commercial systems were introduced. These systems were based on using a laser to “draw” the desired circuit pattern on a photosensitive substrate. The exposed substrate is then developed and etched to create the desired circuit.
Laser direct imaging systems quickly became the preferred method for creating high-density PCBs due to their superior accuracy and resolution. Today, most PCB manufacturers use laser-direct imaging systems to create the desired circuit patterns on their boards.
How does Laser Direct Imaging (LDI) work in PCB?
Laser Direct Imaging (LDI) is a technology that utilizes a laser to expose the desired image onto the substrate directly. This technology is commonly used to produce printed circuit boards (PCBs). To create the desired image, the laser selectively removes material from the substrate. This process is known as laser ablation.
LDI is a process of creating images on a PCB using a laser. It is a direct imaging process, meaning the image is created directly on the PCB without needing a film or mask. This makes LDI ideal for creating small, complex, or high-density images on a PCB. If you are considering using LDI to create images on your PCBs, remember a few things.
- First, LDI is a very precise process, so it is essential to have accurate artwork.
- Second, LDI is best suited for creating small, simple images. If you need to create a large or complex image, there may be better options than LDI.
- Finally, LDI is a relatively new technology, so it is essential to work with a manufacturer that has experience with this process.
LDI is an exact and accurate method of creating images on substrates. It can create very fine details and is often used when high levels of accuracy are required. LDI is also a very fast imaging method, making it ideal for mass production.
There are a few disadvantages to LDI. One is that it can be expensive since it requires specialized equipment. Additionally, LDI is only sometimes compatible with all types of substrates.
What are the advantages of Laser direct imaging (LDI)?
LDI offers several advantages over traditional photolithography, including higher resolution, greater flexibility, and faster turnaround times. In addition, LDI can be used to create images that are impossible to create using photolithography.
There are many advantages of using direct laser imaging in printed circuit boards.
The most obvious advantage is the fact that it is an exact process. This means that the finished product will have very clean and sharp lines and patterns. This is especially important in printed circuit boards because the patterns must be precise to function correctly.
Another advantage of direct laser imaging is that it is a speedy process. This means that large quantities of printed circuit boards can be produced in a relatively short amount of time. This is important for businesses that need to make many printed circuit boards in a short time frame.
Laser direct imaging is also a very flexible process. This suggests that it can be used to produce printed circuit boards with various patterns and designs. This is important for businesses that make printed circuit boards with unique or complex designs.
Laser direct imaging is a perfect process for creating printed circuit boards. It is precise, fast, and flexible, making it an ideal choice for businesses that need to produce high-quality printed circuit boards quickly.
What are the disadvantages of Laser direct imaging (LDI)?
Laser Direct Imaging (LDI) is a technology used for imaging printed circuit boards (PCBs). It is a photolithographic process using a laser to expose the desired image onto a light-sensitive resist-coated PCB. The resist is then developed, and the exposed copper is etched away to create the desired circuit.
There are some drawbacks to using LDI in PCBs. There are several disadvantages to using direct laser imaging in printed circuit boards.
- One of the main disadvantages is that it is a relatively slow process.
- Another drawback is that LDI is a relatively new technology. It is still developing, and there may be some bugs or glitches.
- Additionally, this method can be challenging to achieve high resolutions.
- Additionally, it can be challenging to control the depth of the etches with this method.
- As a result, it is often required to use multiple passes to achieve the desired results, which can further slow down the process.
- Finally, this method can be quite expensive, especially compared to other ways, such as photolithography. LDI is a costly technology. This means that it may only be feasible for some PCB manufacturers to use this technology.
Final Thoughts
Laser direct imaging (LDI) is a technology that utilizes a laser to make an image on a substrate. LDIs are used in various applications, including printing, engraving, and microfabrication. The laser beam is concentrated onto the surface of the substrate, where it vaporizes or ablates the material. The laser beam can be moved across the substrate to create an image.
Share: